Research
✧ Intelligent automation and robotics
● Vision-based agile control
● Interactive robot control
● Safety-critical control
● Active learning and inference
● Formal verification and control
● Motion planning and path following
● Sensor fusion and state estimation
● Computer vision
● SLAM
● Industrial robots, UAVs, automated port cranes, autonomous vehicles
✧ Mechatronic systems and control
● Modelling, learning and system identification
● Energy efficiency optimization
● Disturbance observer
● Motion control
● High bandwidth control
● Vibration suppression
● Nonlinear control
● Model predictive control
● Transport electrification
● Power electronics, machines, and drives
✧ Videos of recent works
● Safety-critical robotic force interaction
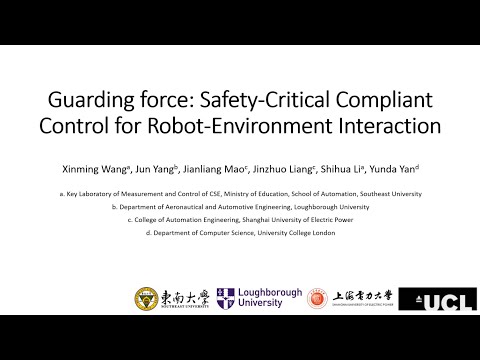
● Dynamic obstacle avoidance of robot
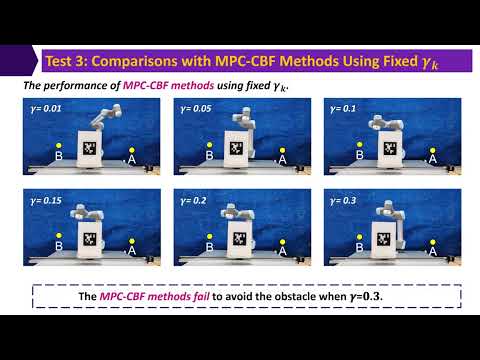
● Safe motion control of underactuated suspension robot
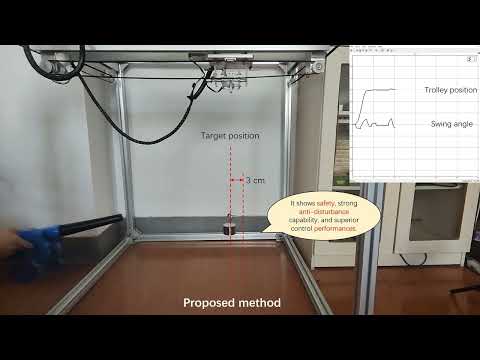
● Safe motion planning of underactuated suspension robot
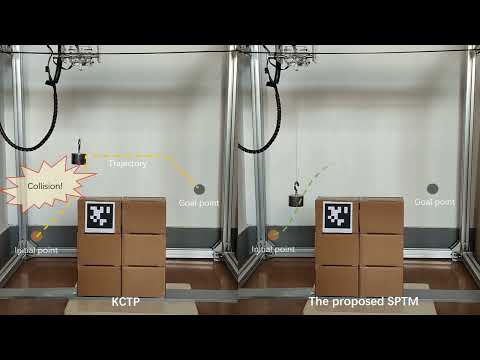
✧ Cases for industrial applications
Case 1: Emerging Autonomous System Technologies for Port Crane Automation
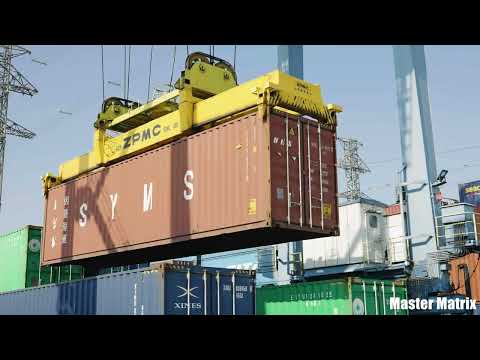
In recent years, Jun has focused heavily on developing emerging autonomous system technologies towards next generation of autonomous systems with higher levels of cognition, agility, safety and resilience. These include many perception, learning and control approaches like visual servo control (e.g., IBVS and PBVS), motion planning, computer vision (e.g., multi-targets detection and tracking), and SLAM. More importantly, many emerging learning and control approaches have been investigated, which include alternating predictive learning, temporal logic control, safety-critical control, active learning and inference, dual control for exploitation and exploration, formal verification and control, etc. The approaches have been extensively investigated or applied to a wide range of automation and robotic systems, e.g., autonomous crane systems in port terminals, interactive robotic manipulators, UAV landing on moving targets, etc.
One impactful typical example is to use the above-mentioned learning and control algorithms to autonomous rubber tire gantry (RTG) crane system for port terminal utilisation. The autonomous RTGs are installed with various navigation and smart sensors like LiDARs, cameras, IMUs, GPSs, and encoders. One the one hand, they need to drive autonomously on the terminal on their prescribed lanes without collision with other objects (e.g., trucks, pedestrians, containers, and other gantries). On the other hand, they have to operate or manipulate (e.g., picking, stacking and dropping containers) autonomously without any human intervention. The barriers include they have a considerable requirement on operation efficiency (human-equivalent or higher working efficiency), robustness (working all day under different weather conditions), and safety (safely interacting with different objectives, such as external trucks, internal trucks, and containers in the yard). The major challenges to realise autonomy lie in difficulty in obtaining target pose due to long disturbance (require less than 3 cm localisation error for over 20 metres detection distance), underactuated dynamics (require anti-sway motion planning, and active anti-swing control), and perception capability limitations (e.g., large perception delay, multi-sensing rate). Some of the mentioned learning and control techniques, e.g., anti-sway control using energy-based motion planning, integrated perceptual control using disturbance observers, safety-critical motion using control barrier function approaches, visual lane detection using deep learning, object detection and tracking using Yolox + DeepSORT, and container yard mapping using SLAM, have been successfully embedded in the AUTANE product of MASTER MATRIX that has been deployed in over 10 RTGs in Shanghai and Ningbo terminals. The first RTG deployed with these algorithms has continuously operated in Shanghai terminal for nearly two years with handling volume over 100,000 containers.
Case 2: High Precision Electric Drives for Intelligent Electrification
Fundamental contributions have been made in disturbance observer-based control (DOBC), nonlinear control, sliding mode control, model predictive control, particularly in unmatched disturbance rejection. These contributions have been extensively applied to power electronics, machines, and drives (PEMD) to promote next generation intelligent electrification. He established a strong track record in applying the developed theoretical and technological innovations (e.g., learning and identification of nonlinearity, disturbance/uncertainty estimation and attenuation, vibration suppression) to industrial systems, particularly electric machines, and mechatronic systems.
One of the most influential examples is the use of these technological innovations to the higher-precision and intelligent PMSM drives in ESTUN company (one of the biggest R&D and manufacturers for electric machines in China). Broadly speaking, the applications include two categories: one is on performance improvement, such as higher position and speed tracking precision, stronger load torque rejection, lower total harmonic distortion, higher control bandwidth, better sensor noise attenuation, etc; and another is on providing new functionalities, e.g., vibration suppression, safe motion, sensor-less control, inertial adaptiveness, parameter auto-tuning, prescribed motion performance, etc. Benefited from the new technologies, the closed loop performance indexes including lower speed fluctuations, lower speed fluctuation amplitude, lower position tracking errors, shorter positioning time, have been enhanced prominently compared to traditional methods. The mentioned control and estimation schemes have been successfully embedded in the AC servo drive products (such as EDC-08 APE,EDB-10 AMA, and ProNet series servo driver products) of ESTUN (DOI: 10.1109/TIE.2016.2583412).